Após a Segunda Guerra Mundial, a Toyota no Japão desenvolveu o Lean Manufacturing, também conhecido como Produção Enxuta. Essa filosofia de gestão visa maximizar o valor para o cliente. Para alcançar isso, eliminamos desperdícios e otimizamos processos produtivos.
A Manufatura Enxuta ou Lean Manufacturing é hoje o modo mais lógico para o desenvolvimento de uma empresa que pensa, por exemplo, em: melhoria contínua, redução de custos, agilidade na produção, maior capacidade produtiva, melhorias do ambiente de trabalho para os funcionários.
Nossa abordagem foca na criação de um fluxo contínuo de produção, assegurando que produzimos exatamente o que o cliente precisa, no momento em que ele precisa (produção puxada).
O que é Lean Manufacturing?
Lean Manufacturing é uma metodologia que busca melhorar a eficiência e a qualidade dos processos produtivos, reduzindo desperdícios e aumentando a produtividade. Através de princípios como a melhoria contínua (Kaizen), a produção puxada (Pull Production) e a eliminação de desperdícios (Muda), as empresas podem alcançar uma produção mais ágil e eficiente.
Aumentar a produtividade não significa comprometer a qualidade. Ao contrário, a alta qualidade dos produtos é prioridade da indústria Lean. Os colaboradores são preparados para solucionar qualquer irregularidade durante a fabricação.
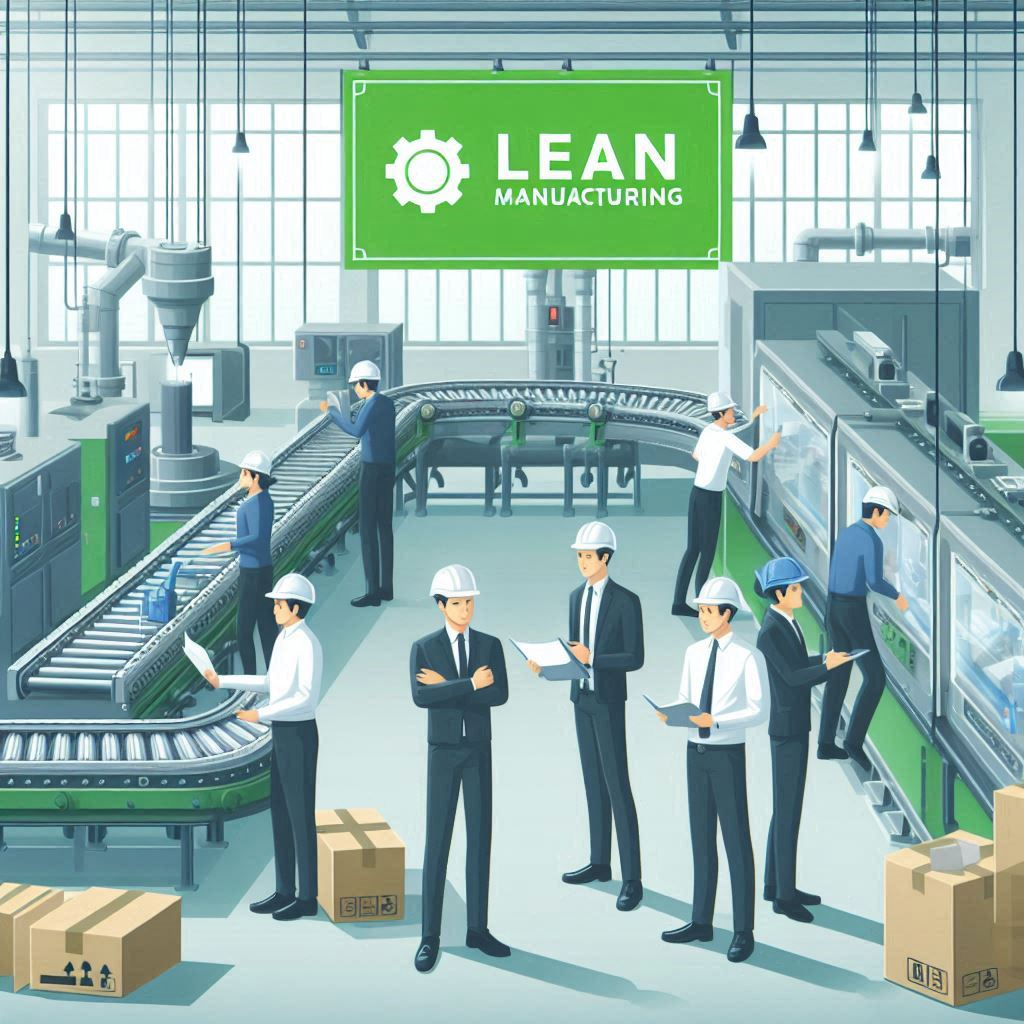
Como Funciona o Lean Manufacturing?
O funcionamento do Lean Manufacturing baseia-se em cinco princípios fundamentais:
1 – Valor
Identificar e focar nas atividades que agregam valor ao produto do ponto de vista do cliente.
Para entender o que realmente agrega valor, é essencial colocar-se no lugar do cliente. O valor é definido pelo cliente, e somente as atividades que transformam diretamente o produto ou serviço de uma maneira que atende às necessidades do cliente são consideradas agregadoras de valor.
Por exemplo, imagine uma linha de produção de bicicletas. Pintar a bicicleta é uma atividade que agrega valor porque a aparência da bicicleta é importante para o cliente. Por outro lado, a movimentação repetida de componentes entre estações de trabalho não agrega valor e deve ser minimizada.
2 – Fluxo
Criar um fluxo contínuo de produção, eliminando gargalos e interrupções.
Criar um fluxo significa organizar a produção de forma que os produtos se movam continuamente entre as etapas do processo, sem paradas ou atrasos. Isso requer a identificação e eliminação de gargalos e a sincronização das atividades para que todas as partes do processo funcionem em harmonia.
Por exemplo, em uma fábrica de montagem de eletrônicos, pode haver uma etapa onde peças esperam para serem testadas, criando um gargalo. Implementar testes automatizados inline pode eliminar esse gargalo, mantendo o fluxo contínuo.
3 – Fluxo Contínuo
Manter um fluxo contínuo de produção para evitar atrasos e desperdícios.
O fluxo contínuo é a prática de produzir pequenos lotes ou peças de maneira constante para manter o ritmo de produção fluido e eficiente. Em vez de produzir grandes lotes que precisam ser movidos e armazenados, a produção contínua minimiza os tempos de espera e reduz o estoque.
Por exemplo, na produção de calçados, em vez de fabricar grandes lotes de solados antes de uni-los ao corpo do sapato, o processo contínuo produziria solados conforme necessários, integrando-os diretamente na linha de montagem para evitar acúmulo de inventário.
4 – Produção Puxada
Produzir com base na demanda real do cliente, evitando superprodução.
A produção puxada usa sistemas como o Kanban para garantir que só produzimos quando há uma demanda real do cliente. Mantemos os estoques em níveis mínimos e desencadeamos a produção apenas pela necessidade imediata.
Por exemplo, em uma pizzaria que adota a produção puxada, os funcionários preparam a massa e os ingredientes à medida que os pedidos são feitos, em vez de preparar grandes quantidades antecipadamente. Isso assegura que as pizzas são sempre frescas e evita desperdício de ingredientes.
5 – Perfeição
Buscar a perfeição contínua, eliminando defeitos e melhorando continuamente os processos.
Perfeição no Lean Manufacturing é sobre a busca incessante pela melhoria contínua (Kaizen). As empresas devem engajar todos os colaboradores na identificação de problemas e na implementação de melhorias incrementais, visando a eliminação completa de defeitos e desperdícios.
Por exemplo, em uma linha de produção de automóveis, incentivamos os operários a parar a linha se encontrarem um defeito (Jidoka). Isso permite a identificação imediata e a solução de problemas, e a melhoria contínua assegura que minimizamos os defeitos ao longo do tempo.
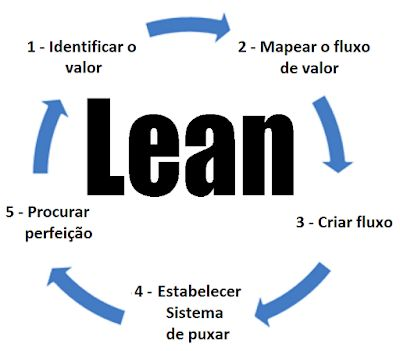
8 Tipos de Desperdícios Identificados no Lean Manufacturing
1 – Superprodução
Produzir mais do que o necessário ou antes de ser necessário. Isso leva ao aumento de estoques e ao desperdício de recursos.
Por exemplo, em uma fábrica de roupas, produzir um grande lote de camisetas que não têm demanda imediata pode resultar em estoque parado, ocupando espaço e recursos financeiros que poderiam ser usados de forma mais eficiente.
2 – Tempo de Espera
Períodos em que os materiais, produtos ou funcionários estão inativos, aguardando o próximo passo no processo.
Por exemplo, se uma linha de produção de eletrônicos tem uma máquina que frequentemente quebra, os operadores podem ficar esperando por consertos, interrompendo o fluxo de produção e aumentando o tempo de espera.
3 – Transporte
Movimentação desnecessária de materiais ou produtos entre processos. Isso não agrega valor e pode aumentar o risco de danos.
Por exemplo, transportar componentes entre diferentes prédios de uma fábrica pode resultar em danos aos produtos e em tempo perdido, além de custos adicionais de manuseio e transporte.
4 – Excesso de Processamento
Realizar mais trabalho ou usar mais recursos do que o necessário para atender aos requisitos do cliente.
Por exemplo, em uma oficina de manutenção, realizar verificações extras ou passos de acabamento que não foram solicitados pelo cliente pode consumir mais tempo e recursos sem adicionar valor ao serviço.
5 – Inventário
Manter um estoque excessivo de matérias-primas, produtos intermediários ou acabados que não estão sendo utilizados de imediato.
Por exemplo, uma empresa que fabrica componentes eletrônicos pode ter um grande inventário de peças que não são utilizadas rapidamente, ocupando espaço e capital que poderiam ser empregados em outras áreas.
6 – Movimentação
Movimentos desnecessários de pessoas dentro do processo produtivo, como andar de uma estação de trabalho para outra.
Por exemplo, em uma linha de montagem, quando os operadores precisam se deslocar frequentemente para buscar ferramentas ou peças, eles desperdiçam tempo e esforço. Portanto, podemos minimizar isso organizando melhor o espaço de trabalho.
7 – Defeitos
Produtos ou serviços que não atendem aos padrões de qualidade e precisam ser retrabalhados ou descartados.
Por exemplo, na fabricação de componentes automotivos, a produção de peças defeituosas que precisam ser retrabalhadas ou descartadas aumenta os custos e o tempo de produção, além de afetar a satisfação do cliente.
8 – Intelectual
Desperdício do potencial humano, como a falta de utilização das habilidades e conhecimentos dos colaboradores.
Por exemplo, em uma empresa de software, não aproveitar as ideias dos desenvolvedores para melhorar os processos ou criar novos produtos pode levar a uma perda de oportunidades de inovação e à desmotivação dos funcionários.
Algumas Ferramentas do Lean Manufacturing
1 – 5S
O 5S é uma metodologia de organização do ambiente de trabalho que visa aumentar a eficiência e a produtividade por meio da limpeza e da arrumação. Os cinco passos são Seiri (Classificação), Seiton (Ordenação), Seiso (Limpeza), Seiketsu (Padronização) e Shitsuke (Disciplina).
Por exemplo, em uma fábrica de eletrônicos, os funcionários utilizam o 5S para organizar suas estações de trabalho, garantindo que apenas as ferramentas e materiais necessários estejam presentes, tudo tenha um lugar definido, e que o ambiente esteja sempre limpo e ordenado.
2 – Kanban
Kanban é um sistema de sinalização visual utilizado para controlar a produção e o fluxo de materiais. Ele ajuda a equilibrar a demanda com a capacidade de produção, evitando excessos e faltas.
Por exemplo, em uma linha de montagem automotiva, cartões Kanban são usados para sinalizar quando mais peças precisam ser produzidas ou requisitadas, garantindo que as peças certas estejam disponíveis no momento certo, sem excesso de inventário.
3 – Kaizen
Descrição: Kaizen é a filosofia de melhoria contínua, onde todos os colaboradores participam ativamente na identificação e implementação de pequenas melhorias nos processos e no ambiente de trabalho.
Por exemplo, em uma empresa de manufatura, os trabalhadores são incentivados a sugerir melhorias em suas tarefas diárias, como a reconfiguração de uma estação de trabalho para reduzir movimentos desnecessários ou ajustar a sequência de operações para aumentar a eficiência.
4 – Just in Time (JIT)
Descrição: O Just in Time é uma estratégia que busca produzir apenas o que é necessário, quando é necessário, e na quantidade necessária. Ele reduz o estoque e melhora o fluxo de produção.
Por exemplo, em uma fábrica de móveis, começamos a fabricar um conjunto de cadeiras apenas quando recebemos um pedido, garantindo que não haja excesso de produtos estocados e que utilizamos os recursos de maneira eficiente.
5 – Value Stream Mapping (VSM)
Descrição: O Value Stream Mapping é uma ferramenta utilizada para mapear todos os passos necessários para levar um produto ou serviço até o cliente. Ele ajuda a identificar desperdícios e oportunidades de melhoria ao longo do fluxo de valor.
Por exemplo, em uma fábrica de produtos alimentícios, a equipe utiliza o VSM para mapear o processo desde a chegada da matéria-prima até a entrega do produto final. Isso permite identificar etapas redundantes e gargalos, implementando melhorias para acelerar o tempo de produção e reduzir custos.
Benefícios do Lean Manufacturing
1 – Redução de Desperdícios: Eliminação de sete tipos de desperdícios: superprodução, tempo de espera, transporte, excesso de processamento, inventário, movimento e defeitos.
2 – Melhoria da Qualidade: O Lean Manufacturing implementa controles rigorosos de qualidade e busca reduzir defeitos por meio de práticas como Jidoka (automação com toque humano) e Poka Yoke (mecanismos à prova de erros). Isso garante produtos de alta qualidade e reduz a necessidade de retrabalho.
3 – Aumento da Eficiência: Processos mais eficientes e fluxos contínuos de produção são características fundamentais do Lean. A adoção de ferramentas como Kanban e o mapeamento do fluxo de valor (VSM) ajuda a identificar e eliminar gargalos, resultando em uma produção mais rápida e eficiente.
4 – Redução de Custos: Ao eliminar desperdícios e aumentar a eficiência, o Lean Manufacturing reduz os custos operacionais. Menores estoques, menos desperdícios e processos otimizados contribuem para uma redução significativa dos custos.
5 – Satisfação do Cliente: Com a produção puxada baseada na demanda real e a entrega de produtos de alta qualidade em prazos mais curtos, o Lean Manufacturing aumenta a satisfação do cliente. Atender melhor e mais rapidamente às necessidades dos clientes resulta em maior fidelidade e reputação positiva no mercado.
6 – Flexibilidade: O Lean Manufacturing permite uma rápida adaptação às mudanças na demanda do mercado. A produção puxada e a abordagem Just in Time garantem que a produção pode ser ajustada rapidamente, sem a necessidade de manter grandes estoques.
7 – Melhoria Contínua: A cultura de melhoria contínua (Kaizen) é fundamental no Lean Manufacturing. Todos os funcionários são incentivados a identificar e implementar melhorias incrementais, resultando em inovação constante e processos cada vez mais eficientes e eficazes.
Aplicabilidade do Lean Manufacturing
Diversas indústrias e setores, incluindo automotiva, manufatura, serviços, saúde, TI e até mesmo projetos de inovação, podem aplicar o Lean Manufacturing. A filosofia Lean é amplamente utilizada para melhorar a produtividade, eficiência e qualidade dos produtos e serviços, além de reduzir custos e aumentar a competitividade.
10 Perguntas com Respostas
1 – O que é Lean Manufacturing?
Lean Manufacturing é uma filosofia de gestão voltada para a produção enxuta, que busca aumentar o valor do produto para o cliente, eliminando desperdícios e otimizando processos produtivos.
2 – Quais são os cinco princípios do Lean Manufacturing?
Os cinco princípios são Valor, Fluxo, Fluxo Contínuo, Produção Puxada e Perfeição.
3 – Por que o Lean Manufacturing é importante?
O Lean Manufacturing é importante porque ajuda a aumentar a eficiência operacional, melhorar a qualidade dos produtos e serviços, e oferecer maior valor aos clientes, ao mesmo tempo em que reduz custos e ganha competitividade.
4 – Como o Lean Manufacturing pode ser implementado em uma empresa?
A implementação do Lean Manufacturing requer uma mudança de mentalidade em toda a organização, desde a alta direção até os operadores de linha. Envolve a identificação e eliminação de desperdícios, a criação de um fluxo contínuo de produção e a produção baseada na demanda real do cliente.
5 – Quais são os benefícios do Lean Manufacturing?
Os benefícios incluem redução de custos, aumento da eficiência, melhoria na qualidade dos produtos e serviços, maior satisfação dos clientes e maior competitividade.
6 – Quais são os principais desafios na implementação do Lean Manufacturing?
Os principais desafios incluem a resistência à mudança, a necessidade de treinamento e capacitação contínua, e a adaptação dos processos existentes para se alinhar com os princípios Lean.
7 – Como a tecnologia pode ajudar no Lean Manufacturing?
A tecnologia pode ajudar na automação de processos, na coleta e análise de dados, na identificação de desperdícios e na melhoria contínua dos processos produtivos.
8 – Quais são os oito desperdícios identificados pelo Lean Manufacturing?
Os oito desperdícios são: Transporte, Estoque, Movimentação, Espera, Superprodução, Processamento Excessivo, Retrabalho e Intelectual.
9 – Qual é o papel da filosofia Kaizen no Lean Manufacturing?
A filosofia Kaizen, que significa “melhoria contínua”, é fundamental no Lean Manufacturing, pois incentiva a participação ativa de todos os colaboradores na busca constante por melhorias nos processos e produtos.
10 – Como o Lean Manufacturing pode ser aplicado em setores não manufatureiros?
O Lean Manufacturing pode ser aplicado em setores como serviços, saúde e TI, focando na eliminação de desperdícios, na melhoria dos processos e na entrega de valor ao cliente.
Conclusão
Concluindo, o Lean Manufacturing oferece uma abordagem poderosa e eficiente para otimizar processos produtivos e melhorar a qualidade dos produtos e serviços. Ao adotar os princípios fundamentais de valor, fluxo, fluxo contínuo, produção puxada e perfeição, as empresas reduzem desperdícios, aumentam a eficiência e respondem rapidamente às demandas do mercado. As ferramentas Lean, como 5S, Kanban, Kaizen, Just in Time e Value Stream Mapping, organizam e tornam o ambiente de produção mais produtivo.
Os benefícios do Lean Manufacturing são vastos. Em outras palavras, as empresas por exemplo, reduzem custos operacionais, melhoram a qualidade, aumentam a satisfação dos clientes e promovem uma cultura de melhoria contínua.
Dessa forma, implementar o Lean exige um compromisso genuíno de toda a organização, desde a alta direção até os operadores de linha, e supera desafios como a resistência à mudança e a necessidade de treinamento constante.
Como resultado, com aplicação adequada e consistente, o Lean Manufacturing se torna um aliado estratégico para empresas que buscam excelência operacional e competitividade no mercado global. Empresas garantem produtos e serviços de alta qualidade e valor agregado para os clientes.